Fasteners pins
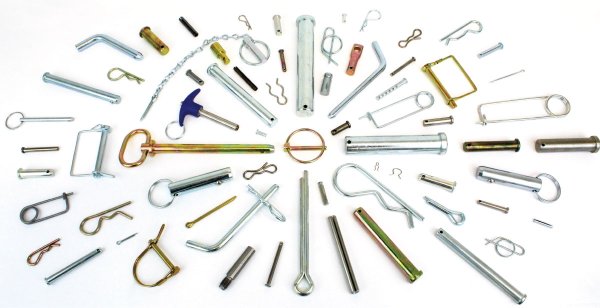
Pin fasteners, or fastening pins, are non-threaded fasteners used to align and connect components in industrial machines, vehicles, electronics, architecture, and many other applications. Pin fasteners pre-date threaded fasteners like screws and bolts by many centuries as the technology to efficiently create screw threads developed much later. Today, they are as common and as widely used as threaded fasteners.
What is a Pin Fastener?
Pin fasteners are primarily used to secure or connect parts in scenarios in which the main forces acting on them are shear forces – opposing forces which push one section of the pin in one direction and another section in the opposite direction.
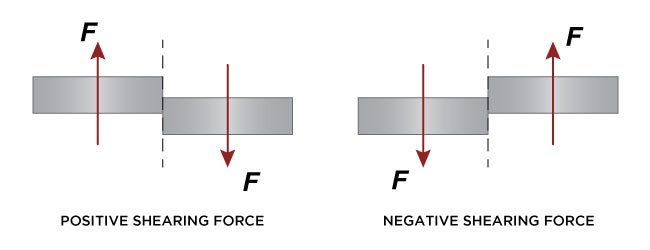
Pins are less suited to applications where they are primarily exposed to axial forces that would pull or push the pin or connected parts in a direction parallel to the pin’s axis. Pins secured by a retaining mechanism – cotter pins or hitch pin clips, for example – can be used in scenarios with some axial force caused by rotation or vibration. However, a threaded fastener such as a bolt is better suited for applications with significant axial forces.
Because pins are used in non-threaded holes, they often require friction or tension to keep them in place. One of the key differences between fastening pin designs is how they are retained.
- Slip fit: There is little to no friction between the pin and the hole as the hole’s diameter is larger than the pin’s diameter. The pin can fall out of or through the hole, so slip fits are not used in through-hole applications unless the pin is retained in another way.
- Press fit: The pin’s diameter is slightly larger than the hole. As the pin is installed, it or the hole deforms slightly, causing both components to exert a radial force that holds the pin in place. Press fits can generate significant holding forces that prevent pins from moving axially, although the axial holding forces are less than an equivalently sized bolt. Press fit fasteners are also known as interference fits or friction fits.
- Spring force: The pins are designed to compress, exerting a spring force against the sides of the hole; examples include
slotted spring pins and
coiled spring pins. - Clips and pins: Retaining clips and pins are inserted through a hole in a larger pin so it can’t pull out. Examples include
bridge pins,
lynch pins, and
cotter pins. - Detents: A detent is a mechanism with a ball or latch that protrudes from the pin’s surface. The detent sits against a spring so it can be compressed during installation and removal. Detents are found in
detent pins and
cotterless clevis pins.
Slip Fit vs Press Fit
Spring Force
Clips and Pins
Unlocked Detent
Locked Detent Pin
How Are Pin Fasteners Made?
Metal fastener pins are formed from metal rods, wires, or sheets. They undergo different processes depending on the type of pin. Manufacturing processes include:
- Cutting:
The rod or wire is cut to the desired size. - Wire forming:
The wire is shaped on a wire forming machine, undergoing processes that include bending, stamping, and upsetting. Learn more about
wire forming and wire forming machines. - Turning:
Larger diameter pins are turned on a lathe. The lathe spins the part at high speeds, and a cutting tool removes material. Turning is used to shape, groove, bore, and part pins. - Grinding:
Pins may be ground to add features such as chamfers or to achieve exact specifications with tight tolerances. This process is essential for pins that will be pressed into place, where precise diameters are essential. - Drilling:
Pins may be drilled to create holes for other fasteners, clips, or detents. - Rolling:
Spring pins are manufactured by rolling metal strips into a tube or coil. - Heat treatment:
Steel pins can be hardened by a process of heating and cooling, which changes their metallurgical properties. - Finishing:
Finishing adds a coating to the pin’s surface. Fastener pins are available with various finishes, including chromate conversion coatings, phosphate coatings, electroplating, and passivation. They are also available as plain, unfinished parts.
Types of Pin Fasteners
There are many different pin fasteners, each with unique characteristics suitable for specific applications. Some of the most common
pin fastener types are:
Dowel Pins
Dowel pins, also known as straight pins, are cylindrical rods used to position or align parts. They have chamfered ends to aid insertion. In many applications, alignment is achieved with two dowel pins set in holes at precise distances on the mating parts. Dowel pins are often used instead of screws or bolts when applications require fast part removal and installation.
Generally, dowel pins should be pressed into place, not hammered. Hammering dowel pins can damage the pin and the hole.
The most commonly used dowel pins are made of steel, including:
- Stainless steel dowel pins
- Alloy steel dowel pins
- Carbon steel and low carbon steel dowel pins
If you need softer or lighter parts, Huyett also stocks
brass and
flat vent dowel pins.
Dowel pin diameter tolerances are precise because fit within the hole is critical to the pin functioning properly. On standard inch dowel pins, the pin is manufactured 0.0002 inches over the nominal diameter. You can expect width tolerances of +0.0001/+0.0003 over nominal, as specified by ASME B18.8.2. For example, a dowel pin with a nominal diameter of 0.25 inches has an actual diameter between 0.2501 and 0.2503 inches. Metric dowel pins have similar tolerances.
In addition to standard dowel pins, there are variations with features to suit specific requirements:
- Flat vent dowel pins are used in blind holes. Pressing unvented dowel pins into blind holes is dangerous because air cannot escape.
- Grooved dowel pins have a spiral groove along their outer diameter. Like flat vent pins, they allow liquids and gasses to escape during installation; however, grooved dowel pins maintain contact with the mating hole around their entire circumference. Grooved dowel pins should not be confused with groove pins, which we’ll discuss later.
- Pullout dowel pins have a threaded hole to attach a pin removal tool to ease extraction.
- Oversized dowel pins are 0.01 inches over nominal diameter. They are used in worn holes.
- Hollow dowel pins are tube-shaped pins that another fastener, such as a bolt, can pass through. They allow for alignment and fastening via the same hole.
Watch our “How to Measure” series videos on how to measure standard and DIN 7 dowel pins:
Want more information on dowel pins? Check out our
Dowel Pin Reference Guide.
Taper Pins
Taper pins are similar to dowel pins, but, as the name suggests, they are tapered along their length – one end has a larger diameter than the other. Taper pins are used as precise positioning pins: the taper allows for very accurate reseating after a part has been disassembled.
Taper pins are available in inch and metric sizes.
Inch taper pins are given a number designation related to the diameter of the widest end and a length in inches. For example, a
#1 by 1-1/2 inch taper pin has a largest-end nominal diameter of 0.172 inches and a length of 1.5 inches. In contrast,
metric taper pin designations refer to the diameter of the smallest end. You can find more information about taper pin sizes and designations in our guide to
Taper Pin Features.
Like dowel pins, taper pins are available with additional features. We stock
internally threaded taper pins and
externally threaded taper pins, both of which provide a tool attachment point for easier removal.
Watch our “How to Measure” series videos on how to measure standard and internally or externally threaded taper pins:
Want to learn more about taper pins? Read our
Taper Pin Information Guide.
Clevis Pins
Clevis pins are non-threaded fasteners that can be used in place of bolts and rivets. A traditional clevis pin has a head at one end and a hole at the other. The pin is inserted through holes in a clevis jaw or
shackle. A cotter pin is inserted into the hole in the clevis pin shaft, securing the pin and mating parts in place. Clevises and clevis pins are used in many industries as an easy-to-install three-part fastening system, including in agriculture, mining, aviation, construction, and sailing. or shackle. A cotter pin is inserted into the hole in the clevis pin shaft, securing the pin and mating parts in place. Clevises and clevis pins are used in many industries as an easy-to-install three-part fastening system, including in agriculture, mining, aviation, construction, and sailing.
In addition to
standard clevis pins, there are many variations on the basic principle:
- Grooved clevis pins feature a groove in place of the through-hole on a standard pin. They are secured with an e-clip or similar fastener.
- Headless clevis pins have no head, and instead have holes at both ends. They are used in applications where the pin can be withdrawn in both directions.
- Universal clevis pins have multiple through-holes so that they can be used with different size clevises.
- Cotterless clevis pins, also known as detent pins, have a detent in place of the through-hole.
Watch our “How to Measure” series videos on how to measure standard, headless, cotterless, and grooved clevis pins:
Want to learn more about clevis pins? Check out our
What Is A Clevis Pin? guide.
Cotter Pins
Cotter pins are wire-formed split pins used to secure clevis pins, shafts, and other components. A standard cotter pin has a teardrop-shaped head and a pair of tines or prongs, one shorter than the other so they can be easily separated. The prongs are inserted into a through-hole and then bent to secure the pin.
Cotter pins are easy to install and remove and are typically reusable. They are widely used in agriculture, construction, and other industries when applications require simple designs and easy in-field assembly and disassembly.
The
standard cotter pin is one of many similar wire-formed pins of the same basic shape.
- T-head cotter pins feature a low-profile head for applications with limited clearance.
- Hammerlock cotter pins are designed to be hammered into place. When the end is hammered, the prongs are forced apart.
- Clinch pins have a self-locking mechanism – the prongs spring apart after the pin is installed.
In addition to variations on the standard cotter pin, many specialist pin designs fulfill the same function.
- Bow tie pins are double-ended pins that can be installed from both sides.
- Ring cotter pins lock securely in place when installed.
- Circle cotter pins are used in applications where a sharp external point is to be avoided.
Watch our “How to Measure” video to learn how to measure cotter pins. For more videos on how to measure each type of cotter pin, check out our
YouTube channel.
Detent Pins
Detent pins are similar to dowel pins, with the addition of a detent at one end and a ring at the other. They are also known as quick-release pins or cotterless hitch pins because they can be quickly installed and removed without a cotter pin. They are ideal for applications where the pin must be removed frequently to adjust or replace parts.
Huyett stocks
inch detent pins in
stainless steel,
carbon steel, and
brass.
Metric detent pins are available in stainless steel.
Positive Lock Pins
Positive lock pins are a more sophisticated alternative to detent pins. In addition to one or two detents, positive lock pins have a locking mechanism that prevents the detents from moving and a button at the top to release the lock. Positive lock pins provide a secure non-threaded fastening solution for applications that require repeated insertion and removal.
Positive lock pins are available in several designs to suit various ergonomic and installation needs:
- Button head positive lock pins
- Ring grip positive lock pins
- L-handle positive lock pins
- T-handle positive lock pins
Watch our “How to Measure” series videos on how to measure positive lock pins:
Groove Pins
Groove pins are similar to dowel pins with the addition of three grooves running parallel to the axis. The grooves are formed in a swaging operation that displaces but does not remove material. When the pin is pressed into a hole, the displaced material is compressed, generating radial forces that hold the pin in place.
Groove pins often have non-grooved pilot areas and are available in many groove and pilot configurations. These configurations are available in both inch and metric (DIN) standards, which have similar features but are not interchangeable.
Some of the groove pin types we stock include:
- Type A / DIN 1471: Full-length tapered grooves for maximum holding pattern
- Type B / DIN 1472: Half-length tapered grooves
- Type C: Quarter-length parallel grooves
- Type D / DIN 1474: Half-length reverse tapered grooves
- Type E / DIN 1475: Half-length parallel grooves located centrally equidistant from the ends
View a
complete guide to groove pin types to learn more. When buying groove pins, be sure to select the type, the correct measurement standard (inch or metric), and the correct size for your application.
Watch our “How to Measure” series videos on how to measure groove pins:
Want to learn more about groove pins? Read our
Grooved Pin Features and Types guide.
Spring Pins
Spring pins – also known as roll pins or tension pins – are rolled metal pins with chamfered ends that, when pushed into a smaller diameter hole, exert a spring force that holds the pin and mating parts in place.
There are two main varieties of spring pins:
- Slotted spring pins are hollow metal tubes with a slot running parallel to the pin’s axis. Upon insertion, the slot closes, and the pin generates a radial holding force.
- Coiled spring pins are formed by rolling a longer strip of metal to form a coil. Unlike slotted spring pins, coiled pins are not hollow.
Watch our “How to Measure” series videos on how to measure spring pins:
Want to learn more about spring pins? Check out our
Introduction to Spring Pins guide.
Snap Pins
Snap pins, also known as wire lock pins and snapper pins, are self-locking pins that incorporate a wire-form locking mechanism, eliminating the need for a retaining pin. They are often used in linkages on power take off (PTO), hydraulic, and hauling equipment, particularly on agricultural machinery.
The simplest form, the
single-wire snap pin, features a wire connected at the head which hooks around the other end, stopping the pin moving laterally out of its hole due to vibration or gravity. Snap pins should not be used in applications where significant axial forces are expected.
Variations on the basic snap pin design have additional features.
- Two-wire or
double-wire snap pins use a pair of wires in the locking mechanism. They are suitable for heavier-duty applications. - Tab-lock snap pins have a tab-shaped bend in the wire to allow for easier removal.
- Tension snap pins use a coiled wire that imparts spring tension to hold the wire in place. Tension snap pins can accommodate higher lateral forces.
Many snap pin varieties are available with both round and square wire locking mechanisms.
Watch our “How to Measure” series videos on how to measure snap, tab, and coil tension pins:
Hitch Pins
Hitch pins, also known as trailer pins, are heavy-duty pins with a swivel handle at one end and a through-hole or groove at the other. They are commonly used to hitch trailers and attach agricultural machinery to tractors and other vehicles. Once installed, hitch pins are held in place by a hitch pin clip (see below) or a lynch pin.
Huyett stocks several types of hitch pins:
- Hitch pins with PVC-coated handles in various colors, including
red and
orange. - Round-handle and
square-handle hitch pins. - Swivel-lock hitch pins with a tab lock that eliminates the need for a mating part to secure the pin.
Watch our “How to Measure” series videos on how to measure hitch pins and swivel lock pins:
Bent Pins
Bent pins are, as the name suggests, heavy-duty steel pins with a 25° bend at one end. The other end features a drilled hole, which takes a bridge pin or a
cotter pin. Bent pins are a low-cost alternative to hitch pins, and they are used for many of the same applications; they are often referred to as bent hitch pins. Bent pins are ideal for connecting equipment that is frequently disconnected and reconnected. or a cotter pin. Bent pins are a low-cost alternative to hitch pins, and they are used for many of the same applications; they are often referred to as bent hitch pins. Bent pins are ideal for connecting equipment that is frequently disconnected and reconnected.
Watch our “How to Measure” series videos on how to measure bent pins:
Hitch Pin Clips
Hitch pin clips are a diverse category of pins and retaining clips that are installed through a hole or in a groove in a larger pin to prevent axial movement. They are primarily used to secure hitch pins, bent pins, and clevis pins in place but can also be used with other types of pin, including headless pins.
- Bridge pins are ridged wire-form pins, also referred to as hitch pin clips or R-clips, which lock into a hole or groove in the mating pin.
- Grip clips, also known as self-locking bridge pins, feature a bent leg that snaps onto the end of a mating pin to prevent movement.
- Hair pins are similar to bridge pins, but they are intended to be fitted over a groove rather than in a hole.
- Various non-pin clips may also be used to retain pins, including
e-clips and
x-rings, both of which fit into grooves on a mating pin’s shaft.
Lynch Pins
Lynch pins, also known as linchpins or click pins, are self-locking pins used to hold parts on shafts, axles, and other pins. Lynch pins feature a wire ring designed to exert a spring force against the pin’s shaft. When the ring is installed in a hole at the end of a shaft or pin, the ring snaps down over the end of the mating part, locking it in place.
Lynch pins are stronger than cotter pins and bridge pins, and they are often employed in heavy-duty applications on agricultural three-point hitches or to attach wheels and bearings to shafts.
Find the Best Pin Fastener for Your Project with Huyett
Huyett stocks a vast assortment of pin fasteners and retaining clips. To find the perfect pin for your project, view the full selection of industrial fastening pins on huyett.com and visit our
Pins and Wireforms FAQ.
People also ask
what do pin fasteners look like?
Pin fasteners, also known as clevis pins or cotter pins, consist of a straight metal pin with a circular head on one end and a small loop or hole on the other end. The pin is inserted through aligned holes in two objects to hold them together. A separate cotter pin, a bent piece of wire with two prongs, is then inserted through the loop or hole, securing the pin in place and preventing it from sliding out.