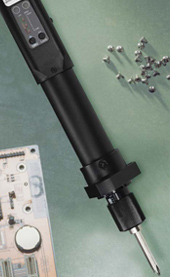
For many manufactures, the assembly process can signify one of the highest direct labor costs. These costs can be tremendously reduced through automation. Today’s fastening process is really about providing quality torque control for manufacturers with a greater ability to achieve repeatable performance, optimize production and remain cost competitive.
As manufactures look to improve assembly and manufacturing practices, the manual fastening methods of applying torque are advancing more and more toward automated torque tools. Automated screwdrivers provide manufactures with a rapid, reliable and precise method of fastening screws. Precise torque measurement and control can be challenging when using manual electric and pneumatic torque screwdrivers, but the new technology with automated screwdrivers has led to tighter process control and higher quality standards, while keeping costs down.
Selecting the proper automated torque screwdriver requires a comprehensive analysis of production requirements by the manufacturer. Enhancing efficiency and productivity are key elements for developing a value-added assembly strategy. Other items that need to be considered when reviewing automation equipment are:
Benefits of Assembly Automation
- Reducing the production cycle
- The tool can be easily reconfigured and adapted for new production projects
- Provides a consistent repeatable process and eliminate potential variations
- The tooling costs provides favorable return of investment
- The ergonomic benefit eliminates the tedious and repetitious manual process performed by operators
- Maintenance and repair are easy and low cost
Robotic Screwdrivers
Designed for robotic and automated applications, the BFA-Series and NFA-Series electric screwdrivers feature a high performance brushless motor design that provides durability and reduces the standard maintenance costs associated with electric screwdrivers. The durable robotic screwdrivers deliver reliability and precise torque control. These automated screwdrivers feature an automatic shut-off clutch system that stops fastening once torque is achieved. The screwdrivers are ESD certified, ensuring less than 1 Ohm at the bit tip. ESD management with a power tool ensures product quality, cost savings and a reduction in overall ESD failures. Manufacturing engineers involved with microelectronic products are aware of the importance of controlling Electrostatic Discharge (ESD) failures.
Mountz offers the next generation of automation and process control in screw fastening technology. The SH-Series, SD-Series and HD-Series are a versatile torque and automation control systems engineered for precision accuracy and repeatable torque control.
Designed for automation and robotic fastening applications, the SD-Series and HD-Series are technically innovative and advanced fastening solutions. The electric screwdrivers feature a high performance Swiss Maxon brushless motor design that provides durability and reduces the standard maintenance costs for electric screwdrivers. The SD-Series is intended for low torque applications and the HD-Series is equipped to handle light & medium fastening applications. Mountz offers various hand held and robotic models that range from 0.08 – 13 inch-pounds for the SD-Series tools and a torque capacity range of 4.4 – 86.8 inch-pounds with the HD-Series tools.
The SH-Series is robotic screwdriver system that is built with an AC servo motor system. The torque is controlled by the motor’s current, which provides precision torque control. Designed for both critical low and high torque fastening applications, Mountz offers various automation models that range from 0.43 – 564.2 inch-pounds.
These torque control systems deliver cost savings and quality benefits through useful features such as digitally adjustable torque setting, variable torque and speed control, multiple I/O options for integration with PLC and other line control techniques. A Windows-based software package that can customize each fastening application is included with the product. The torque control system features a built-in error-proofing data and screw counter. Multiple fastening strategies can be implemented for sensitive and/or difficult assembly joints. These automation tools increase productivity as one tool can be programmed to do the job of multiple conventional tools; saving time, maintenance cost, space and training.
Automated screwdrivers are ideal for automotive, aerospace, packaging, electronics, appliances, biomedical, & medical fastening applications. If you need to automatically install screws, then automate your fastening process. Minimize design and manufacturing costs with an automated screwdriver to enable your product to be offered at an competitive market price.
Controlling torque is essential for companies to ensure their product’s quality, safety and reliability isn’t compromised. The failure of a three-cent fastener that isn’t properly tightened can lead to catastrophic or latent failures. Fasteners that are insufficiently fastened can vibrate loose and excessive torque can strip threaded fasteners. Using a quality automated screwdriver system has become increasingly important for many companies to ensure that proper torque is being applied and maintain requirements associated with the ISO 9001 quality standard.
Improve your fastening process today and reduce your manufacturing costs. Have a Mountz representative visit your facility and provide a product demonstration. Request an appointment today.